Indicating instruments are analogue devices that show the quantity that is measured on a graduated scale using pointers. They are classified based on their basis of operation and the forces operating on them.
Classifications on indicating instruments
Basic classification.
Electromechanical | Here the electrical signal is translated to mechanical movement as means for indication |
---|---|
Electronic | Giving very fast output which follows the static and dynamic characteristics of the measurant |
Based on principle of operation
Essential features For precise operation of indicating instruments are, 1. Deflecting force, 2. Controlling force, 3. Damping force.
Deflecting force
This force is responsible for moving the pointer from the ZERO position where the pointer is in absence of an input. Deflecting system or moving system that carries out this force is usually converting a electrical input to an mechanical output.
1. Magnitude effect When current passes through the coil it produces a magnetic field. When a soft-iron piece is brought near this coil it is magnetized. Depending upon the current direction the poles are produced in such a way that there will be a force of attraction between the coil and the soft iron piece used in moving iron attraction type instrument. Similarly If two soft iron pieces are near a current carrying coil there will be a force of repulsion between the two soft iron pieces. Which is used in the moving iron repulsion type instrument.
2. Force between a permanent magnet and a current carrying coil
A current carrying coil placed under the influence of magnetic field of a permanent magnet will deflect due to force produced between them. This principle is utilized in the moving coil type instrument.
3. Force between two current carrying coil
two current carrying coils placed closer to each other repulses eachother. If one coil is movable and other is fixed, the movable coil will move away from the fixed one. This principle is utilized in electrodynamometer type instrument.
Controlling force
Controlling system produces a force that produces the deflection in the pointer proportional to the input magnitude. Without this, the pointer once deflected will keep moving till the maximum position irrespective of the input magnitude. The function of the controlling torque are:
- Produce a force equal and opposite to the deflecting force at the steady (final) position to make the deflection of the pointer unique for a particular magnitude of input.
- To bring back the moving system back to zero when the factor causing the deflection is removed. Without this, the pointer stays in its maximum position without moving back to zero.
1. Spring control: Hair spring made of phosphobronze provides a restoring torque directly proportional to the angle of deflection(θ) when it twists. At equilibrium Tc = Td Ie Tc α θ. For this the spring should have large number of coils so the deflection per unit length is negligible and the deformation is not permanent. Characteristics of the spring:
- Non-magnetic
- Resistance to fatigue
- Low specific resistance
- Low temperature coefficient
2. Gravity control Weights are used to balance the motion of pointer. Adjusting the weight by screwing up and down helps with the control. Torque produced is proportional to sinθ , where θ is the displacement of pointer from null position. Tc = k sinθ
Advantages of gravity over spring control
- Cheap
- Not affected by temperature
- Not susceptible to fatigue with time
Disadvantages of gravity control
- Cramped scale ( non linear )
- Instrument needs to be vertical
Damping force
Both the deflecting system and the controlling system act with inertial forces, thereby there is always an overshoot from the desired value. The pointer always shoots from O to A and then deflects back to B moving to and fro gradually reducing its amplitude before settling on the correct position of O. This is because with the deflecting Td and the controlling forces Tc being equal in magnitude and opposite to each other at the point A, Tc > Td, it moves back to B where Td > Tc.
Damping forces are employed to provide a damping effect on this oscillation to settle the pointer much faster, and an equilibrium is achieved smoothly.
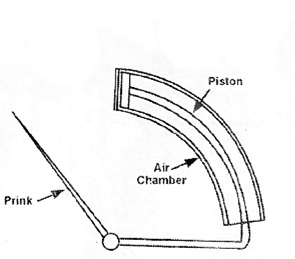
2. Fluid friction damping In the place of air, fluid is filled such as mineral oil. But the principle is the same as air friction. The vane mounted on to the moving system is completely immersed in the oil. The oil provides the damping effect on the vane. Being much denser, they provide greater damping forces. They are used in electrostatic type instruments
Design precaution: The oil, which is a good insulator, should not
- evaporate easily
- have any corrosive effect on metals.
- Have its viscosity change much with temperature.
Advantages of fluid friction damping:
- Good insulation by oil
- Less strain on the spindle and no frictional error
Disadvantage of fluid damping:
- They can only be placed in vertical position.
- Oil leakage
- Not portable
3. Eddy current damping Eddy currents are localized loops of current induced in the conductor due to the change in the magnetic field, perpendicular to the magnetic field. These induced currents produce magnetic fields of its own that counter acts the magnetic field that created the current in the first place. Used largely in PMMC, they cannot be used in places where magnetic field affects the system like moving iron and dynamometer.
Methods of eddy current damping
- A metal former that carries the working coil
When the spindle rotates, the disc cuts the magnetic field between the damping magnet producing eddy current. ( A moving coil in magnetic field produces current)
- A thin disc attached to the moving system, that moves in the field of permanent magnet.
Eddy currents are induced in the metal former which when the coil tries to move exerts a damping force on it,